While downtime is inevitable, it does not have to be a detrimental factor to your production line productivity. As we step into 2023 with new production goals, we’ve compiled a list of 10 tips that can help you reduce downtime – or avoid it all together – in regards to container handling aspects of your line.
1. Schedule Your Downtime
One of the best ways to stay on top of downtime is to plan for it. Schedule your breaks in production, changeovers, or maintenance, and relay them to your team as well. This way you are able to stay on the same page, and you are never surprised with halted production. You can also use this downtime to accomplish tasks that ordinarily could not be possible while your line is running.
2. Label Your Change Parts and Screws
If you have incorporated change parts on your line you are probably familiar with the time it can take to changeover your line for a new container size. You can improve this process by labeling your change parts and color plugging your timing screws. Help avoid any confusion and cut down on operator errors by identifying each part and its corresponding partner.
Change Parts labels should clearly identify the container they run and the
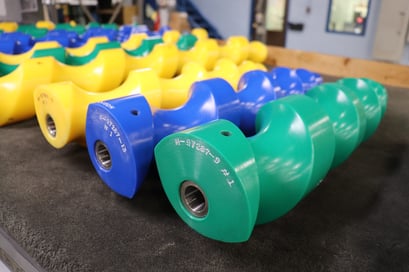
machine they are to be placed on. When labeled correctly and clearly, it can reduce operator confusion of where to place the parts and for which container size. It takes out the guess work and speeds up the changeover.
Another way this can be done on your timing screws and change parts is through color plugs. These small UHMW inserts are coordinating to a container sizes, giving a quick visual to the operator which part or screw needs to be run on the line. For example, green might mean the 14 oz while blue denotes the 6 oz.
3. Parts Carts
While your goal is to be as efficient and productive as possible, our goal is to provide you with all of the tools you need to make this a reality. Half the battle of changeovers is knowing where your change parts are located in your facility, Parts Carts help optimize this organization process.
By incorporating a Parts Cart, you can also profit from a variety of benefits like:
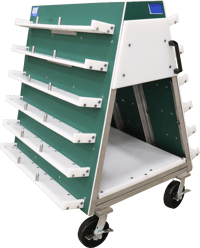
- Easy Loading and Unloading
- Reduced Changeover Time
- Clearly Labeled and Identifiable Parts
- Damage Prevention
- Quick Washdown
- Saving Valuable Floor Space
- And More!
Store your extra change parts all in one location with utility carts to expedite the manufacturing process and address all of your operation’s productivity needs.
4. Stock Up on Spare Parts
With all industries experiencing longer lead times you do not want to wait until wear items fail to order spare parts.To help keep your line and your machine up and running, we recommend evaluating your inventory and stocking wear components. When you stock them ahead of time, you can schedule maintenance or quickly get back up and running in the event the machine fails.
Learn more about stocking Morrison’s wear components here.
5. Preventative Maintenance Agreements
Unplanned downtime can be costly, and we understand that you want your lines running as long as they can, and as frequent as they can. While surprises happen, we advise implementing preventative maintenance care to help cut down on those surprises. For example, your line is getting jammed between applications and damaging product, upon further investigation you noticed a screw that needed to be tightened. The problem is fixed, and your line is back up and running, but you now have to clean and dispose all of the damaged product. While this halt in production was not detrimental to your throughput, it could have been avoided completely with a simple planned maintenance check. Understanding and making a schedule dedicated to checking in and tweaking your machines can not only help prolong your machines lifetime, but help your line stay as precise and accurate at the day it started running.
That's why included in all of our products is Support Built In®, our personal customer service program
for any general questions you may have or technical support you may need before, during, and after installation. Our Aftermarket Services department offers Preventative Maintenance Agreements (PMA) designed to keep you up and running before a problem arises on your line. Unlock the full power of Support Built In®, schedule and plan for maintenance checkups.
To learn more about this product, click here.
6. Train Your Operators
Train your operators to catch things that can damage or halt your line production.
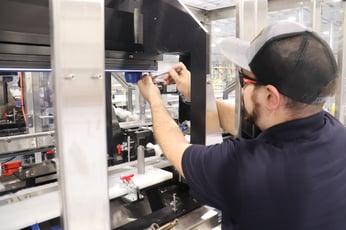
For example, a problem arises on your line and unfortunately no one onsite is equipped to fix the problem. Now you have to stop production until a maintenance team can arrive and asses the problem causing a longer break in production. Whereas, if your operators had base level knowledge of what to look for in maintenance, this problem could have been handled swiftly, or even better avoided completely.
7. Down Bottle Rejects
There are many times that companies deal with inefficiencies and downtime due to containers falling over on the production line. Instead of having a person standing on the line looking for a down container, it is much more cost effective and efficient to implement a down bottle reject to kick off any containers that have already fallen down.
To learn more about this product, click here.
8. Quick Change Rails
Are changeovers taking up precious time on your line? Quick Change Over Rails help speed up the process by helping take the hassle out of changeovers. Color coated to match container size; these components act as change parts on your line. For example, the picture displaying the square container on the left is the current container on your line. When it's time to run your round bottle, you simply swap out your rails that are all stamped with their appropriate color and location, producing changeovers in minutes.
Want to take it to the next level? Morrison offers rail storage solutions that can be built into machines with each cubby labeled for the corresponding change part.
9. Morrison Auto Adjust Rails®
As you know, changeovers can be the biggest factor of downtime costs, while it is a necessary function on most lines, it does not have to be so stressful. How many times have you had to stop production and send a crew to dangerous heights just to adjust your conveyor rails while trying to run another container size?
With automatic conveyor rails, you say goodbye to long breaks in production and unsafe changeovers for your team.
You can learn more about this partnership and installing it on your line here.
10. Deluxe Adjuster
In addition to the other tips we have talked about, a great addition to your timing screw drive units would be a deluxe adjuster. The deluxe adjuster allows for a tool-less adjustment of timing screw centerlines, which is a huge factor during changeovers. Without deluxe adjusters, operators need to manually adjust the centerline of the drive units and screws, which leaves much room for human error that can have a significant impact on your container handling.
With a deluxe adjuster on your line operators simply adjust the relationship of the conveyor, screw and container with the handwheel or ratchet to a pre-determined number corresponding with that container, providing correct screw centerlines and improved container handling in a fraction of the time.