Some of the most laborious processes on packaging production line involve inverting. When performed manually, this process can be a cost-eating task that slows down the throughput potential of your line.
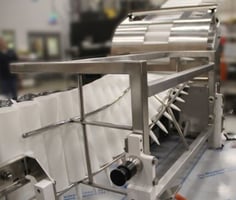
However, sometimes containers just need to be flipped over for the downstream application, so you place a person on the line whose sole task is to invert the containers one way or another. This is unreliable and can cause speed inefficiencies.
As container handling experts, we automate the inverting process with our Morrison twist assembly drive units. Morrison twist timing screw assemblies are custom designed to your container and the application we are inverting for on the line. Taking into account upstream and downstream equipment, we utilize UHMW or metal twists that are washdown compliant when needed and can handle the speeds you need to up your output while decreasing labor needs.
Think it can’t get any better? When you’re running more than one container on a line, these twists and screws can become change part items to make for simple and easy changeover. Inverting on your existing conveyor is one of the many container handling solutions manufacturers know exist, but the possibilities on how they can improve your processes are impressive for your ROI.
Here’s a sample of the inverting projects we’ve engineered in the last 50 years.
The Morrison Twist for Basic Inverting:
When the upstream equipment deposits the container onto the conveyor on one side, but the downstream equipment needs it to be upside down or right side up, this is where these twist systems can really make a difference. Depending on your container, Morrison would design an UHMW plastic twist or a metal twist that takes the containers and flips them to the opposite side right on your existing conveyor, preparing the container to be accepted by the next packaging application.
Inverting Rinsing Machines:
Bottle rinsing is a necessary process for glass sterilization, especially for wineries. This process is time consuming but required. Morrison carefully handles the bottles at high speeds in our rinsing inverting systems, often minimizing breakage in the process and allowing more bottles to be rinsed in a shorter period of time. See it in action here:
Inverting for Code Dating:
Flip your containers up and back down just for code dating! In these systems, we utilize our twist technology to bring the container up and set it back down while the code date is applied as the necessary side becomes exposed. This automates this process and like the other systems can often fit on your existing conveyor layout.
With timing screws, one rotation of the screw is one container discharged, so using this simple mathematical equation, we can line up our system to your code dating machine easily. A video speaks more than our words, so see a system like this in testing here:
Sanitation and Sterilizing:
Another requirement in food safety is the sterilization of a cap on a bottle or jar. Think of pasta sauce. The heat of the sauce after filling and capping can be utilized to sanitize the cap of the jar. You just need a way to flip these containers upside down for a period of time. Our twist systems would mount on your existing conveyor, allowing you to automate this process. As the jar enters the twist, it inverts the sauce onto the cap, allowing the heat transfer to take place.
The application can be use for a variety of products where sanitization is necessary.
Stacking:
Do you need to place two containers on top of each other? It seems like a mundane task, but it needs to get done.
Maybe it is to create a multi-pack that goes into a carton or maybe you need to stack your granola on top of your yogurt. In either case, these needs can benefit from twist solutions.
In both situations, we utilize the conveyor to run underneath the twist while one lane of product is fed into the twist and the other underneath it. Timing the screw to the conveyor, we match the containers together. As the one lane feeds into the twist, inverting to be upside down, it will be discharged right onto of the other lane of product, automating this process. Our experts can even integrate other technology in order to seal the two containers together if needed.
What does this mean for you?
A lot of the time, container handling processes are neglected on production lines, and these processes can be the most beneficial to automate due to the labor they require. Chances are, your line can benefit from container handling with Morrison’s experts. Fill out this form and we’ll evaluate your operation to see if twists, or other applications, might be the right solution to improve your throughput.