Pack Expo Chicago 2022 is almost here! Come visit Morrison Container Handling Solutions at booth #4906. To make the most out of your Pack Expo experience, we’ve put together a quick guide to familiarize yourself with what you can expect to see from us in Chicago. Remember to add us to your Show Planner.
Machine #1: The Ice Cream Loop (Pick and Place with Alternate Inverter)
The Ice Cream Loop consists of a Pick & Place system and an Alternate Inverting System.
Pick and Place Breakdown
The pick and place operation follows the linear speed of the screw and picks out containers from the screw. It uses continuous motion to follow the position of the screw and grab containers. Running continuous motion increases the lifespan of the machine and lowers the total cost of ownership (TCO) of the machine. As you may know, a pick and place machine with an indexing motion is hard on the equipment and can make container handling more difficult.
The positive control of the timing screw allows us to know the exact position of the container each moment. This control eliminates the need for complex vision and robotics systems.
Alternate Inverter Breakdown
The alternate inverter uses continuous motion and inversion of containers, creating an alternate inverted pattern of containers. Other approaches you may have seen require an indexing motion to create the alternate inverted pattern, or significantly more conveyor space to divide, invert one lane, and combine into one common lane downstream. This alternate inverting system is servo driven, allowing for the most robust and positive container handling. Morrison’s approach of a standardized design, allows for easy length modification for future machine designs, minimizing potential future engineering time.
When it comes to the conveyor, it’s preferred for Morrison to supply a new conveyor, but it can be mounted to existing conveyor if required. Morrison’s zero-gap conveyor side transfer design and approach eliminates gaps and dead plates creating a smooth transition between conveyor chains and allowing for efficient container handling.
The perimeter guarding on the entire system is a small overall footprint. The gull wing door design allows for full access to the machines without being extremely invasive to the greater line layout. It also features safety interlocked doors.Machine #2: Smart Changeover Machine
Our Smart Changeover Machine runs multiple container sizes around a loop, manipulating the containers in different ways. The system is equipped with A.I. Operator Assistance that helps ensure that the operator sets the system up correctly.
A color sensor looks at the color of the change parts and automatically loads the proper recipe, so setup positions are correct by adjusting centerlines (both vertically and horizontally) as well as inputting the proper speed settings. This reduces changeover time and operator error.
The system also automatically times the timing screws. When performing changeover or setting up the line, the screws will automatically time to the correct location so that you don’t have to rely on an operator to visually inspect and set the timing between screws.
There is a low total cost of ownership of the system. The eccentric drive bracket allows for minimal parts, meaning lower preventative maintenance parts. This also allows for visible inspection of the belt and pulley for easy preventative maintenance. Destaco clamps are used on the idler end to remove the screw, making changeovers completely tool-less.
Around the conveyor loop of the system are Morrison Auto Adjust Rails®. With a push of a button on the HMI, and no tools needed, you can change over the rail locations to handle a wide variety of container sizes. This allows for infinite adjustment of rail position for many container sizes to run on the same line.
The loop features two operations depending on the container run.
- Square containers are turned 90 degrees as they pass through the set of timing screws before going around the loop to run through the screws again.
- Round containers are dwelled in the timing screw for a split second at a consistent location while the screw continues to run, which in time adds life to the machine.
Possible Applications for this Machine:
- Label placement on a different side of a container
- Inspection of different sides of the container
- Presentation of containers to the end of line equipment
- Inspection of a stable product
- Weighing of a container over a scale
- Applying a label
- Dropping glue onto containers
- Pressing a cap or plug onto the containers
Machine #3: Smart Combiner and Divider Loop
This dynamic system divides containers on the fly based on the product demand downstream. This system allows you to take an upstream process that’s running at a faster speed and release the product into two lanes for a downstream operation that requires multiple lanes. It can also be used in a scenario where the downstream operation requires two machines to keep up with the upstream operation, like a filler upstream that can run faster than the downstream labeler.
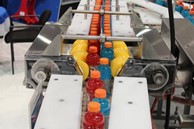
The design of the system implements a tool-less changeover to allow for multiple container sizes to run on the system. With four servo motors, this system allows for automatic phasing of the timing screws to divide the containers accordingly into the appropriate lane. The system also utilizes an inspection station to look at the color of the containers to divide them into the appropriate lane.
- Runs speeds over 1000 containers per minute.
- Maintains positive control of the container.
- Can lower maintenance costs.
- Compact footprint easily fits into existing lines.
- Can be implemented into an inspection/rejection station.
- Robust eccentric drive bracket minimizes spare parts required.
Overall, this Smart Divider system allows for ongoing and dynamic production with the ability to automatically shift containers to the appropriate lane.
This dynamic timing screw system combines round or oval containers from two lanes into one common lane. The combiner can run each lane independent from one another, instead of relying on both lanes requiring a backlog of containers. The system works by releasing containers 180 degrees out of phase and railed together on the discharge of the system. This system is even offered with an upgraded design that allows for containers to be fully combined in the timing screw.
- Able to mount to existing conveyor.
- Minimizes maintenance.
- Robust eccentric drive bracket minimizes spare parts required
See these systems in action at Pack Expo Chicago 2022. Add us to your Show Planner and make an appointment to meet directly with our experts while at Pack Expo.
Have you registered to attend PACK EXPO International yet? Use our free COMP Code 75C35 and register here.